Droped ye ol switch yesterday. The good news is the L buttond decided to cushion the fall so there was no major damage. Bad news is it sacrificed the solder joint of the button in the process.
I can replace it with this but have a solder iron and I'd like to learn how to do some of this small soldering (is this considered "micro" soldering?). It's a cheap adjustable temp solder pen from Amazon, but, as you'll see, it gets hot. Normally I try to heat both parts to the same temp with a little flux and a dab of solder and voila! It's soldered. But with this tiny little board I don't see much in the way of a metal pad to solder to and I'm just melting the shit out of the button and globbing solder all over. Is this something that can be done? I'm probably going to be ordering a new ribbon/button part shortly and use that in the end, but I figured this might be good practice.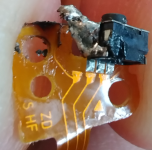
I can replace it with this but have a solder iron and I'd like to learn how to do some of this small soldering (is this considered "micro" soldering?). It's a cheap adjustable temp solder pen from Amazon, but, as you'll see, it gets hot. Normally I try to heat both parts to the same temp with a little flux and a dab of solder and voila! It's soldered. But with this tiny little board I don't see much in the way of a metal pad to solder to and I'm just melting the shit out of the button and globbing solder all over. Is this something that can be done? I'm probably going to be ordering a new ribbon/button part shortly and use that in the end, but I figured this might be good practice.
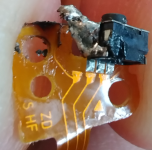